HORA DE PENSAR NA MANUTENÇÃO!
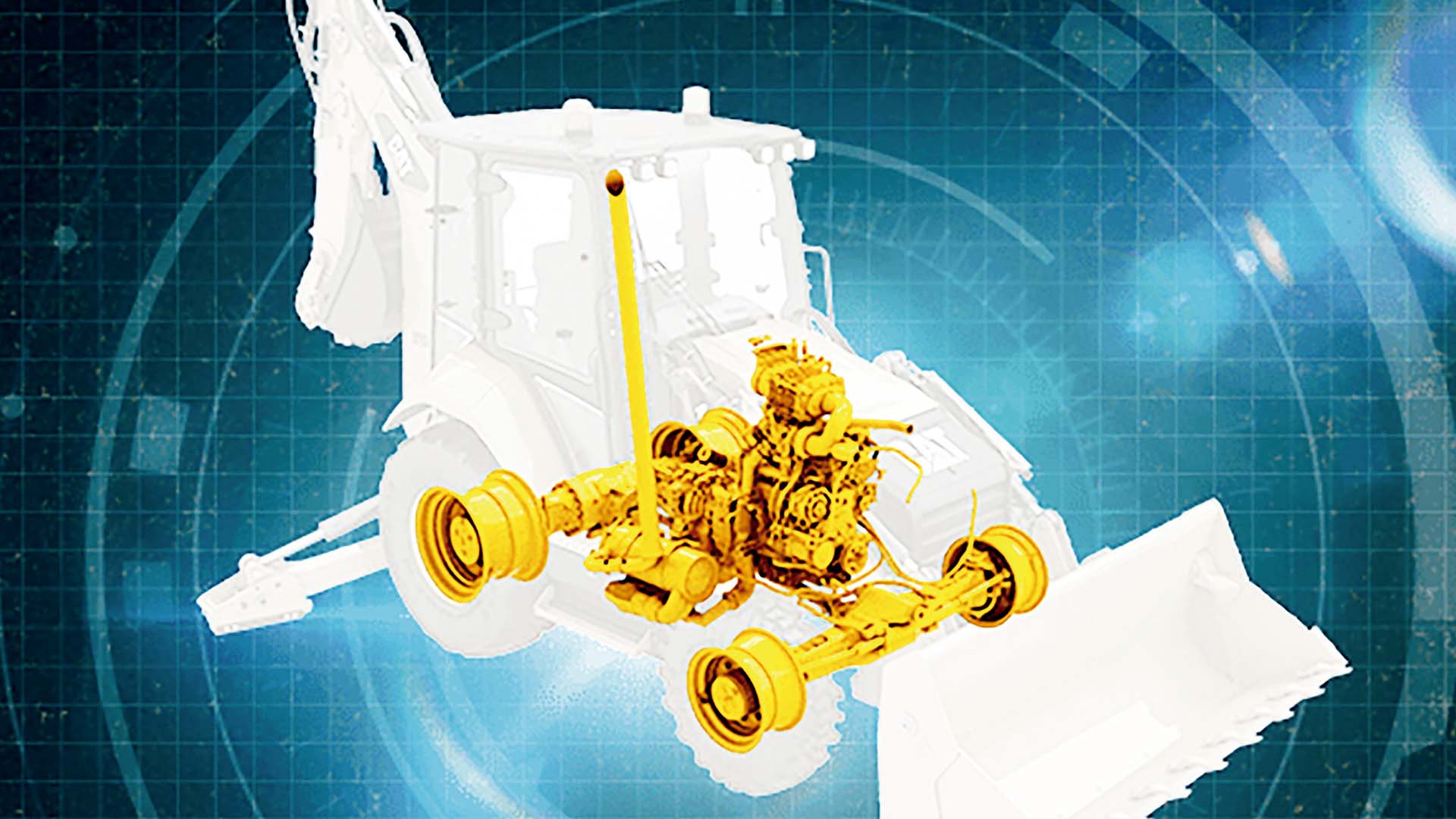
Planejar a manutenção preventiva da frota é um caminho para se evitar gastos maiores em consertos não previstos
Planejar a manutenção dos equipamentos é a única maneira do locador evitar problemas repentinos e interrupções no trabalho. De acordo com os especialistas, o ideal é manter um plano de manutenção bem elaborado, com cronogramas seguidos à risca, utilizando peças e fluidos recomendados pelo fabricante, além de profissionais capacitados para operação e manutenção.
Além disso, quem planeja a manutenção preventiva consegue evitar gastos maiores decorrentes de consertos não previstos. As pás-carregadeiras, por exemplo, são máquinas que ficam constantemente expostas a operações severas por transportarem diferentes tipos de materiais. Portanto, algumas peças sofrem mais desgaste e precisam ser protegidas da sujeira resultante do trabalho.
Os cilindros são principais peças responsáveis pelo esforço de carregamento, assim como os pinos e buchas da caçamba e do braço do equipamento. A falta de lubrificação nestas partes pode resultar em um desgaste prematuro e, em casos mais extremos, causar acidentes e prejuízos durante a obra.
Os pneus também exigem cuidados e não podem ser deixados de lado. Caso haja algum imprevisto com estas partes, os custos de manutenção acabam ficando muito mais elevados. “Um exemplo claro de cuidado com os pneus é seguir a pressão correta para calibragem estabelecida pelos fabricantes. Além disso, o local de operação da máquina deve estar livre de materiais cortantes”, reforça Edson Greggio, diretor geral da Automec/ JCB.
Etapas da manutenção
De acordo com Edson, o plano de manutenção preventiva de pás-carregadeiras estabelece que sejam trocados filtros e fluidos, além da limpeza, lubrificação de pinos e buchas, inspeções e regulagens periódicas de bicos injetores e válvulas do motor, calibragem de pneus, além de análises de óleo e diálises.
“Os processos de lubrificação e inspeção devem ser frequentes e devem constar na agenda diária de trabalho. As intervenções mais avançadas, como as que envolvem substituição de peças e lubrificantes, geralmente são feitas por distribuidores autorizados ou oficinas especializadas”, explica Greggio.
Além disso, o operador precisa ter uma série de cuidados na hora de utilizar o equipamento, porque alguns setores movimentam materiais que podem danificar o sistema da pá-carregadeira. “Dependendo do tipo de material movimentado, as pás-carregadeiras precisam utilizar acessórios de proteção para amenizar os impactos agressivos causados pela entrada de pó no sistema elétrico e nos conectores eletrônicos. Um dos métodos para se proteger terminais e sensores elétricos e eletrônicos, reduzindo efeitos corrosivos, é fazendo aplicações de silicone”, orientou Edson Greggio.
Ele recomenda que os usuários pesquisem o possível teor corrosivo contido no material onde a carregadeira trabalha e descubram se ele pode danificar o equipamento. Desta forma, é preciso tomar medidas de precaução. “Há frotas de carregadeiras que trabalham com adubos e fertilizantes, por exemplo, e nesses casos precisam ter a caixa eletrônica blindada, assim como as máquinas que movimentam palha de cana devem utilizar kits de proteção e ser equipadas com caçambas maiores. A palha seca pega fogo com facilidade, se entrar em contato com o motor”, avaliou.
Braço de escavação
As retroescavadeiras estão entre os equipamentos mais versáteis por terem maior possibilidade de receber implementos. Por isso, requerem um plano de manutenção bem elaborado, que precisa estabelecer intervalos mais curtos ou extensos, dependendo das condições de operação. O trabalho com excesso de carga, a utilização de caçambas, martelos ou implementos inadequados apressam o desgaste da máquina e a necessidade de manutenção.
“O braço de escavação é a parte da retroescavadeira com maior vulnerabilidade, por representar um terço de sua estrutura física. Nele se encaixa o braço, é montada a lança e a mesa de giro, além de serem instalados os implementos. Essa articulação é suscetível a problemas de folgas em pinos e buchas”, observa Edson Greggio.
Se forem instalados rompedores hidráulicos mal dimensionados na máquina, eles podem desencadear problemas no braço de escavação, como trincas e desgaste prematuro de pinos e buchas. Mário Neves, gerente de desenvolvimento da área de equipamentos compactos da Wacker Neuson, diz que a manutenção deve se diferenciar não pelo tipo de equipamento, mas por sua aplicação. Carga horária de trabalho, implementação com rompedores e locais de uso são determinantes.
“Uma retroescavadeira pode ser aplicada em diferentes setores, em tarefas onde o desgaste pode ser menor ou maior que na construção. Se trabalhar em uma planta de fertilizantes, por exemplo, a máquina estará exposta a material corrosivo e vai precisar de lavagem diária. Alguns componentes vão precisar ser substituídos com mais frequência, a retroescavadeira precisará de blindagem do alternador e proteção de sistema elétrico”, explica Mário.
Preventiva e preditiva
Essencial para a vida útil dos equipamentos, a manutenção preventiva evita problemas decorrentes das horas trabalhadas e condições de uso do equipamento. Ela pode ser associada à manutenção preditiva, baseada no acompanhamento periódico das máquinas, análise de dados coletados por meio de monitoramentos ou inspeções em campo. Desta forma, é possível verificar pontualmente cada equipamen- to e antecipar eventuais problemas.
Relton Henrique Cesar, gerente de serviço da Case Construction Equipment, acrescenta que também são necessárias análises de óleo, diálises e telemetria, para obter um quadro completo das condições do equipamento, o que previne falhas. “Em uma revisão que envolve a troca do óleo hidráulico, por exemplo, de 30% a 40% do óleo per- manece na máquina em cilindros, válvulas e mangueiras.
Durante o funcionamento da máquina, existe a possibilidade de surgirem focos de contaminação provenientes de mangueiras substituídas, tampas de reservatórios abertas, ou trocas de vedações. Nesses casos, as análises de óleo ajudam a monitorar as condições do fluido quanto à aditivação e nível de contaminação. Já a diálise auxilia na limpeza do fluido que circula no sistema”, explica o especialista.
De acordo com ele, é preciso evitar paradas não programadas. Interromper o carregamento antes do horário programado ou iniciar mais tarde do que o previsto compromete consideravelmente o resultado final dos trabalhos. “Outro fator que deve ser evitado é o aumento do tempo de ciclo do equipamento. Além de não significar diretamente um ganho na produtividade, a medida ainda pode comprometer o rendimento do trabalho, seja pelos operadores ou pela capacidade do maquinário”, arremata.



Postado em 17/12/2018